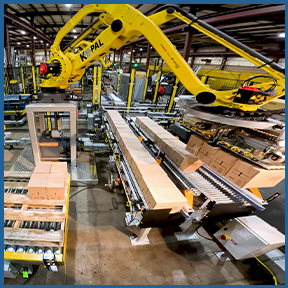
Palletizing, Stretch Wrapping, Transfer Car and Labeler System for Multiple Lines
Our customer required a system comprising four complete production lines, from palletizing and securing loads to labeling them in sequence so that they would be double-stacked in the correct order at the end of the line. Kaufman successfully designed and built this system utilizing four FANUC M-410i C / 185 robots, four turntable stretch wrappers, and one FANUC LR Mate 200i D robot fitted with labeling/verification functionality.
Contact Us Today for information on what Kaufman Engineered Systems can do for you!
System Details
OVERVIEW:
This system consists of four product lines with independent palletizer cells fitted with four FANUC M-410i C / 185 robots and four independent stretch wrapping cells utilizing Kaufman turntable stretch wrappers. The entire system then employs the use of one transfer car that conveys stacks of empty pallets to each cell as well as offloading finished unit loads to the material handling line. Completed, secured loads reach then sequence through the labeling cell, which utilizes one FANUC LR Mate 200i D enabled with labeling and verification functionality, ensuring that like product load will be double stacked with like product load at the end of the line.
DETAILED SYSTEM INFORMATION
Within each separate production line, the palletizing operation begins with the system operator loading the necessary dunnage materials into the system. Once the system has been charged with dunnage, the palletizing sequence starts with a FANUC M-410iC/185 picking an empty pallet from the pallet stack and placing it in the build position. Cases then begin being conveyed to the robot at approximately 120-180 feet per minute (FPM). Once accumulated within the robot “pick” location, the M-410iC robot utilizes a multiple-zoned vacuum end effector to pick and place the cases onto the pallet following the appropriate build pattern. This process will repeat until a completed unit load is built. The completed load is then conveyed to the staging location within the wrapper cell.
The EXPA-15 Turntable Stretch Wrapper proceeds to securely wrap the unit load at 15 rotations per minute (RPM), utilizing a load lifter at the end to secure the load directly to the pallet before lowering once again so that the completed pallet can be conveyed out of the wrapper cell to await pickup from the transfer car.
The transfer car acts as a shuttling conveyor that offloads finished loads to the material handling line; palletized loads then run through the labeling cell utilizing a FANUC LR Mate 200iD in sequence so that like product winds up being double stacked with like product at the end of the line. The transfer car also carries empty pallets to each production line to replenish the staging area for the M-410iC robots to restock the palletizing cell at the beginning of each load.
As always, Kaufman personnel designed, built, and tested the system thoroughly in-house before performing Factory Acceptance Testing (FAT) to obtain customer sign-off. Our entire process is designed to allow us to successfully complete turnkey installs and start-ups of our finished systems.
Find out how Kaufman Engineered Systems can increase your productivity, lower your labor costs, and improve safety at YOUR facility:
Contact Us ---- JOIN OUR MAILING LIST ---- Request Quote