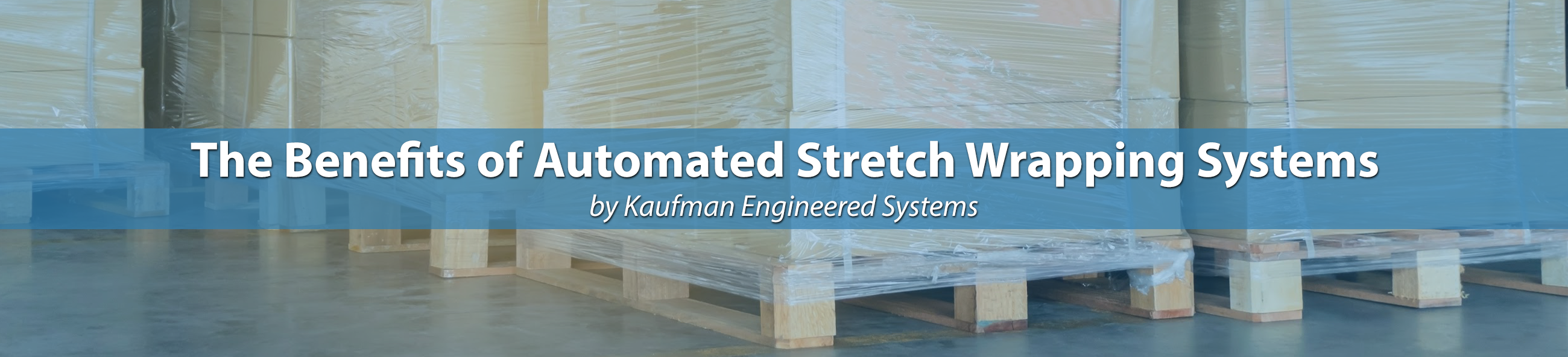
Introduction to Automated Stretch Wrappers
Automated stretch wrappers play an important role in warehouses and distribution centers around the world. They provide an efficient and cost-effective way to wrap palletized loads of any shape, size, and weight. Automated stretch wrapping systems are a great investment for businesses looking to reduce labor costs, increase productivity and improve safety in their facilities.
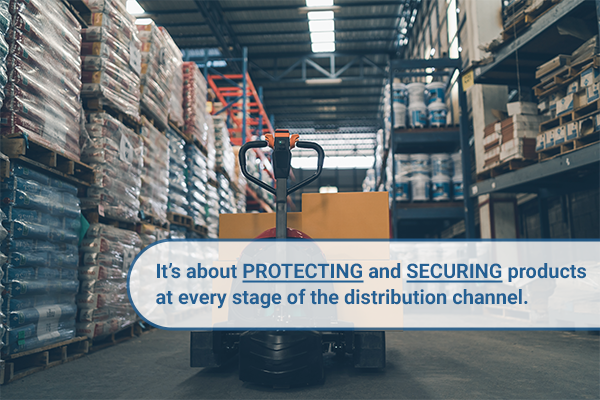
One of the main benefits of automated stretch wrappers is their ability to be placed inline and wrap palletized loads quickly and accurately. This eliminates the need for manual labor, which can be time-consuming and costly. Additionally, automated stretch wrappers can adjust to different sizes and shapes of loads, making them ideal for businesses with varying product sizes.
Another advantage of automated stretch wrappers is that they are designed to use less film than manual wrapping methods. This means that businesses can save money on packaging costs while still ensuring that their products are securely wrapped. Additionally, automated stretch wrapping systems help reduce waste by using only the amount of film needed for each load.
Automated stretch wrappers also offer increased safety benefits compared to manual wrapping methods. By eliminating the need for workers to manually lift and move heavy loads, businesses can reduce the risk of workplace injuries and accidents. Furthermore, automated stretch wrappers help improve worker morale by taking away tedious tasks from employees and allowing them to focus on more important tasks within the warehouse or distribution center.
Overall, automated stretch wrappers offer a variety of benefits that make them a great investment for any business looking to increase efficiency and reduce costs in their warehouse or distribution center operations. With their ability to quickly and consistently wrap palletized loads using minimal film, as well as their safety benefits over manual wrapping methods, investing in an automated stretch wrapping system is a smart decision for any business looking to streamline its operations and save money in the long run.
KForce Automatic Stretch Wrap Series
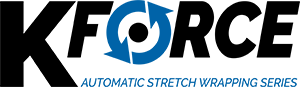
Kaufman Engineered Systems is revolutionizing the way businesses package and ship their products with our KForce line of automated stretch wrapping systems. With a variety of options available, including corner board options, corner anticipation mode (CAM), hold-downs, load lifters, plows, and roping, these machines provide an efficient and cost-effective means of consistently securing palletized loads.
What are these various options and modes for Stretch Wrapping?
Corner board options allow for the use of corner boards on each side of the pallet to provide extra stability and protection during transport. Corner Anticipation Mode (CAM) is used to anticipate the corners of the load so that the machine can better apply film to unstable loads. Hold downs offer additional stability to unstable loads during the stretch wrapping process, while load lifters are used to raise the load up so that the wrapping can reach the entire pallet at the bottom of the load. Plows are used to automatically fold additional protection over the top of the load and/or underneath the load, and roping provides the option for rolling the film up to form a rope that is then wrapped around the load for additional strength, increasing the stability of the load.
There are several different types of wrapping models available with KForce automated stretch wrapping systems. The standard KForce models use rotary arm stretch wrapping so that the palletized products remain stationary while the arm rotates around the pallet, securely wrapping it at either 20 RPM (revolutions per minute) or 35 RPM, depending on product stability and cycle time requirements. Any standard KForce model has corner board options available. The KForce T20 model is an automated turntable stretch wrapping system where the palletized load rotates at 20 RPM while the stretch head remains stationary, only moving up and down as it wraps the turning load.
More About Rotary Arm Automated Stretch Wrappers

Rotary arm stretch wrappers are an efficient and cost-effective way to package products for shipping. They provide a secure wrap around the product, protecting it from damage during transit. The rotating arm of the machine wraps the palletized load in a continuous film of stretch wrap, creating a tight seal that keeps the contents safe and secure.
Rotary arm stretch wrappers are ideal for wrapping unstable loads, as they keep the pallet load stationary while wrapping. This ensures that the product is securely held in place and won't shift during transport. The machines are also equipped with a photo eye built into the stretch head, which detects the height of the load, allowing these systems to accommodate different height loads with no operator intervention.
For businesses looking to reduce labor costs, automatic rotary arm stretch wrappers are available, which require minimal operator input. These machines can be programmed with specific parameters, such as the number of wraps per pallet or desired tension level, allowing for consistent results every time.
Overall, rotary arm stretch wrappers offer proficient means of securely wrapping products so that they are protected during storage and shipping. With their ability to firmly hold products in place and optimize wrapping patterns, these machines can help businesses save time and money while ensuring their products arrive safely at their destination.
Video Examples:
More About Automated Turntable Stretch Wrappers
The Perfect Solution for Low-Volume and Medium-Volume Packaging Needs
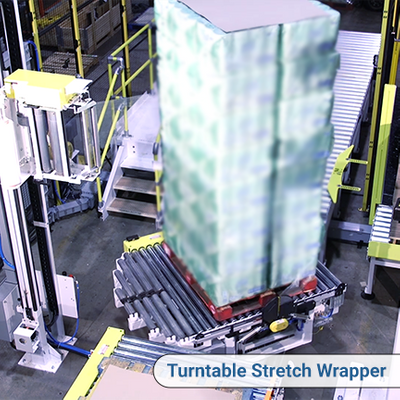
Turntable stretch wrappers are a great option for businesses looking to package their products in an efficient and cost-effective way. These machines use the turntable to rotate the palletized load while the film carriage remains in place, moving up and down to dispense the film wrap and secure the load. For semi-automatic turntable systems, ramps make it easier to load heavy pallets onto the turntable with a pallet jack.
The turntable style is one of the most popular types of stretch wrappers available on the market today. It is designed to be used with stable loads, making it ideal for low-volume and medium-volume packaging needs. The turntable also provides full control over the wrapping cycle, allowing you to customize your packaging process according to your specific needs.
In addition to providing an effective solution for packing products, turntable stretch wrappers also offer a number of other benefits. They are typically less expensive than rotary arm models and have a smaller footprint, making them perfect for businesses with limited space. They also require minimal maintenance and operate automatically. Finally, they offer the ability to integrate with a palletizer to wrap while stacking a load.
If you’re looking for an efficient and cost-effective way to package your products, then a turntable stretch wrapper may be just what you need. With their innovative design and easy operation, it’s no wonder why these machines are so popular among businesses of all sizes.
Video Examples:
More About Corner Boards on Stretch Wrapped, Palletized Loads
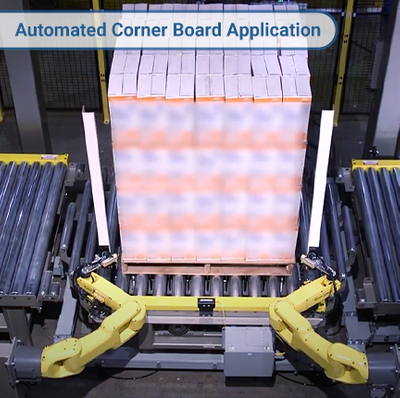
Corner boards can be an essential part of palletizing freight and ensuring that the load is secure and protected during transport. They protect the edges of the pallet from strapping, stretch film, dents, abrasions, and other damage associated with shipping. Corner boards also help to stabilize the entire load and improve stacking strength. KForce corner board placement is automated using Fanuc Robots, which increases precision in the placement of the corner boards onto palletized loads during the stretch wrapping process.
Strapping may not always be necessary when using corner boards. However, when used in conjunction with stretch wrapping, they provide an even more secure solution for protecting your freight during transport. The combination of these two methods ensures that your goods arrive safely at their destination without any damage or loss of product integrity.
In conclusion, corner boards can play an essential part in protecting freight and ensuring that it is secure during transport. They provide a cost-effective way to protect your goods from damage while also improving stacking strength and stability. Automated robotic systems can also be used to increase precision in palletizing loads with corner boards.
Video Examples:
Kaufman’s KForce Series of Stretch Wrapping Systems are custom tailored to meet the specific needs of each and every customer. Whatever options discussed in the paper are needed, we can deliver results that will reduce your labor costs, increase your productivity and improve the safety of your facilities.