Chain Conveyors in Industrial Manufacturing and Distribution Processes
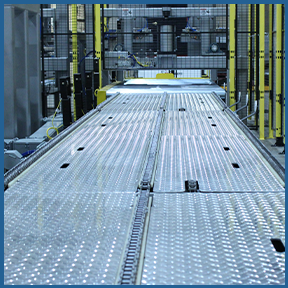
A chain conveyor with a third strand added to the center of the conveyor to better support the pallet/slab/base of the load.
Chain conveyors are widely used in industrial manufacturing and distribution because they are extremely sturdy. This makes them suitable for many applications, especially in harsher conditions and exposure to corrosive products such as salt. This page delves into the design principles, applications, and advantages of chain conveyors utilized in automated systems.
BASIC DESIGN AND WORKING PRINCIPLES
At its most fundamental, a chain conveyor consists of one or more chains that run parallel to each other, pulling materials along a designated path. Based on the application requirements, these conveyors can be designed with single or multiple strands of chains. The chains move around sprockets positioned at either end of the conveyor, driven by motors. Materials to be transported sit directly on the chains or on pallets, fixtures, or carriers attached to the chains.
TYPES OF PRODUCTS & OPTIMAL OPERATING CONDITIONS
Chain conveyors are particularly adept at transporting heavy or bulky items that might damage less robust conveyor types. This includes metal parts, automotive components, large containers, palletized goods, and more. They thrive in environments where durability is key—such as high-temperature conditions, areas with significant debris, or applications requiring the movement of sharp or hot products that could compromise other types of conveyors.
PHYSICS & MECHANICS BEHIND CHAIN CONVEYORS
Chain conveyors function by transferring kinetic energy from the motor to the chains, which in turn propels the materials being transported. The design is optimized to distribute weight evenly across multiple contact points, thereby reducing strain on any single point within the system. This unique feature enables the smooth transportation of heavy loads over extended distances, a task that might pose challenges for belt or roller conveyors due to their limitations in weight capacity and the potential for material slippage or sagging.
Chain conveyors offer superior durability and load capacity compared to other conveyor types. Unlike belt conveyors, they are not prone to slipping under heavy loads, and unlike some roller conveyors, they can easily accommodate hot or abrasive materials without damage.
Request Quote ---- JOIN OUR MAILING LIST ---- Contact Us
Applications in Automated Robotic Systems
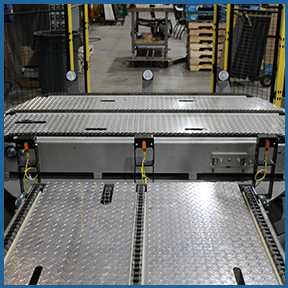
Chain conveyors integrate seamlessly with automated robotic systems across various phases of the manufacturing and distribution process:
Packaging & Palletizing: Robotic arms, with the support of chain conveyors, can safely pick products and precisely place them into packaging or stack them on pallets for shipping. This process is particularly beneficial when handling heavy or cumbersome items, ensuring the safety and reliability of the operation.
Securing and Labeling: For securing operations, automated machinery can wrap or tie down products on chain conveyors, ensuring they remain stable for transport or further processing. Automated labeling systems also work well with chain conveyors, as the predictability and uniform speed of movement allows for precise label application.
Depalletizing: Similarly, automated systems can efficiently remove products from pallets delivered via chain conveyors for unpacking or further processing. The ruggedness of chain conveyors ensures they can handle the returning pallets or waste materials without the risk of damage.
INTEGRATION WITH OTHER CONVEYOR TYPES
Implementing a comprehensive transport system often requires combining chain conveyors with other conveyor types. For instance, delicate items might initially be transported on belt conveyors to a packing area, where they are then moved onto chain conveyors for palletization and shipping. In another scenario, roller conveyors might feed items into a position where robots place them onto chain conveyors for heat treatment or painting processes.
Advantages and Examples
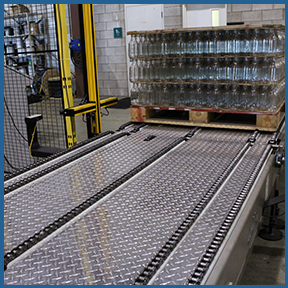
The primary advantages of chain conveyors include their high durability, ability to transport a wide range of products, and compatibility with harsh operating conditions. For example, in the automotive industry, chain conveyors transport car bodies through paint shops, where the conditions could quickly degrade less robust systems. In the aerospace sector, large components are moved on chain conveyors for assembly, highlighting the system's capacity for handling significant weight and size.
In conclusion, chain conveyors are indispensable in modern industrial manufacturing processes. Their robust design and ability to handle diverse products and integrate with automated systems make them a key component in enhancing efficiency and productivity across various industries. Manufacturers can create highly effective and efficient automated systems for handling a broad spectrum of products by understanding the principles behind chain conveyors and leveraging their strengths.
Back to List of All Conveyor Types
Request Quote ---- JOIN OUR MAILING LIST ---- Contact Us