Integrating Conveyor Solutions into Robotic Automation Systems
In the evolving landscape of manufacturing and distribution, the integration of conveyor systems into robotic automation stands out as a pivotal strategy for enhancing efficiency, reducing costs, and improving overall productivity. Conveyor systems serve as the backbone of material handling, providing seamless movement of goods through various stages of production and distribution. Kaufman Engineered Systems specializes in delivering innovative conveyor solutions tailored to meet the unique demands of each automation system.
AUTOMATION SYSTEMS RELYING ON CONVEYOR SOLUTIONS
Robotic Palletizing and Depalletizing: Conveyor systems transport products to robots with end-of-arm tooling that stacks the incoming products onto pallets for shipping or storage and reverses the process for incoming goods. The integration of conveyors to move products to and from packaging stations is crucial for handling high volumes of product with speed and precision.
Packaging Lines: Conveyors move items through packaging stations where robots apply wraps, labels, or seals. The precision and speed of conveyor systems ensure that products are correctly aligned and paced for robotic packaging equipment.
Sorting and Distribution: Automated conveyor systems quickly sort and route products based on size, weight, destination, or other criteria. This is essential in manufacturing and distribution facilities where efficiency and consistency determine the speed and accuracy of delivering goods.
Request Quote ---- JOIN OUR MAILING LIST ---- Contact Us
Types of Conveyors & What They Do
1. Motor-Driven Conveyors & Gravity Conveyors: Motor-driven conveyors utilize motors to move belts, rollers, or chains, providing consistent and controllable movement of goods across manufacturing, packaging, or distribution processes. They are used for transporting a wide range of items, especially where precise speed control or the ability to move products uphill is required. In contrast, gravity conveyors rely on the force of gravity to move items and are typically used for the downward transport of items or in areas where manual assistance can guide the movement, such as assembly lines or loading docks. Both types can interact seamlessly within a facility; motor-driven conveyors can feed items onto gravity conveyors for efficient downstream processing, combining automated control with energy-efficient gravity transport to optimize material handling systems.
2. Mobile Transportation Conveyors: Various types of automated vehicles with conveyor systems or platforms that are designed to move materials or products horizontally or in predetermined paths across manufacturing or distribution facilities. In robotic automation systems for packaging and material handling, they are used to efficiently transport goods between different processing or packaging stations without the need for fixed conveyor lines, allowing for flexible layouts and optimizing floor space.
3. Belt Conveyors: Perhaps the most common type, belt conveyors consist of a continuous belt that operates over rollers. They are ideal for moving products of various sizes and shapes. They are highly versatile and can be used to transport items horizontally, at an incline, or at a decline. Belt conveyors can be either ribbed or smooth depending on the application and they can be utilized to brake/meter product to create specific gapping during the packaging process.
4. Case Conveyors: These systems use a series of rollers to move goods in cases. They can be gravity-fed (where products move by force of gravity) or powered. These conveyors are best suited for handling items with a solid base and are commonly used in packaging and assembling lines.
5. Chain Conveyors: Featuring a series of connected links or chains, these conveyors are designed to transport heavy loads and are often used in automotive and heavy machinery industries. They are particularly useful for moving large or hot items that might damage other types of conveyors.
6. Chain Driven Live Roller (CDLR): Robust conveyor systems that use chains attached to rollers to move products along the production line. They are particularly suited for heavy or rugged loads, including pallets, drums, and other large items, providing efficient transport and handling in manufacturing, warehousing, and distribution applications.
7. MatTop Conveyors: Also known as modular tabletop conveyors, they consist of interlocking plastic modules that create a continuous, flat surface suitable for transporting a wide variety of products. They are highly versatile and used in numerous manufacturing and distribution industries for applications that require gentle handling, easy cleaning, and the ability to accommodate curves and inclines within the conveyor path.
8. Slat Conveyors: Industrial conveyor systems that feature a flat surface composed of discrete slats attached to a chain. They are designed to transport bottles, cans, palletized goods, and heavy or large objects such as metal sheets through manufacturing, assembly, or packaging processes, providing stability and support for products that require a firm base during conveyance.
9. Skatewheel Conveyors: Lightweight, flexible conveyor systems driven by gravity and made up of small wheels mounted on axles and arranged in tracks. They are ideally suited for moving light to medium-weight items with flat bottoms across distribution centers, packaging lines, or assembly areas. This type of conveyor allows for easy manual movement or gravity flow of goods in various directions, including curves, inclines, and declines. This solution is also ideal for areas where product accumulates and requires 0 back pressure, with wheels rolling while products remain stationary.
10. Load Lift & Lift-and-Turn Conveyors: When loaded pallets need to be elevated between different heights a section of the conveyor can be specialized to raise and lower to receive and deliver loads seamlessly through the system. Alternatively, when a load needs to be reoriented to face a different direction before moving through the system, a lift-and-turn feature can be implemented. Click the link to find out more about these adaptable and flexible conveyor solutions.
Benefits of Automation Systems with Integrated Conveyor Solutions
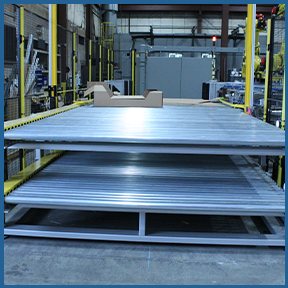
Integrating conveying systems into robotic automation enhances the efficiency and throughput of manufacturing and distribution processes. Here's how:
- Seamless Transfers: Conveyors work in tandem with robotic arms to ensure smooth transfers of materials from one stage of production to another, minimizing handling times and reducing the potential for product damage.
- Increased Speed: Automated conveyors can operate continuously, significantly increasing the speed at which products are moved and processed.
- Precise Positioning: Advanced sensing technology allows conveyors to precisely position items for subsequent automated tasks, such as assembly, inspection, or packaging, thereby enhancing the accuracy and quality of operations.
- Customization and Flexibility: Modern conveying systems can be custom-designed to meet specific operational needs, including adjustable speeds, paths, and integration with other automated systems. This flexibility allows for scalable solutions that grow with the business.
Boosting Productivity and ROI
The adoption of conveying systems within robotic automation projects presents numerous benefits:
- Reduced Labor Costs: By automating material transport, companies can significantly reduce their reliance on manual labor, leading to substantial cost savings.
- Enhanced Safety: Automated conveyors minimize the need for human interaction with potentially hazardous materials or machinery, thereby improving workplace safety.
- Improved Throughput: The speed and efficiency of automated conveying systems result in higher throughput rates, enabling businesses to meet increased demand without compromising quality.
- Lower Operational Costs: Conveying systems contribute to lower overall operational costs through reduced labor requirements, improved safety, and minimized product damage.
- Greater ROI: By enhancing productivity and efficiency while reducing costs, conveying systems provide a strong return on investment, making them a wise choice for any manufacturer or distributor looking to optimize operations.
The Expertise of Kaufman Engineered Systems
In today's competitive industrial landscape, the implementation of conveying systems within a robotic automation framework is not just an option—it's a necessity for manufacturers and distributors aiming for peak efficiency, safety, and profitability. By understanding the types of conveying systems available and their potential applications, businesses can tailor their automation strategies to meet their unique operational needs, paving the way for enhanced productivity and a robust ROI.
Integrating conveyor systems into robotic automation offers numerous benefits, from enhanced operational efficiency to reduced production costs. Kaufman Engineered Systems stands at the forefront of this technological evolution, offering tailored conveyor solutions that meet the dynamic needs of the manufacturing and distribution industries. With a focus on innovation, reliability, and customer satisfaction, Kaufman continues to lead the way in transforming industrial automation landscapes.
Request Quote ---- JOIN OUR MAILING LIST ---- Contact Us