Understanding Conveyor Systems in Robotic Automation: Motor-Driven vs. Gravity Conveyors
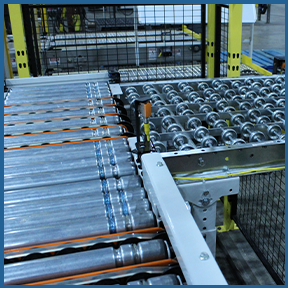
In the realm of robotic automation, conveyors are indispensable components that facilitate the continuous and smooth movement of products throughout the manufacturing process. They play a pivotal role in enhancing efficiency, reducing manual handling, and optimizing the flow of materials from one point to another. Given their significance, it's essential to choose the right type of conveyor system that aligns with the specific needs of a manufacturing process. This article dives deep into the two main types of conveyors - Motor Driven and Gravity Conveyors, highlighting their differences, advantages, disadvantages, and applications.
The Role of Conveyors in Automation Systems
At its core, a conveyor system is designed to transport items across different stages of production or assembly without the need for manual intervention. In the context of robotic automation, conveyors integrate seamlessly with robotic arms, sorters, sensors, and other automated equipment to create a cohesive and high-speed production line. This not only accelerates the manufacturing process but also minimizes errors, enhances safety, and improves overall product quality.
Request Quote ---- JOIN OUR MAILING LIST ---- Contact Us
Motor-Driven Conveyors: Types and Applications
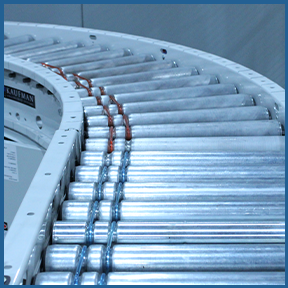
Motor Driven Conveyors are powered by motors which provide continuous movement and enable precise control over speed and direction. They are well-suited for tasks requiring consistent speed, rapid transportation, or uphill movements. Here are some common types:
1. Belt Conveyors: Characterized by a continuous belt material looped over a series of rollers, belt conveyors are versatile and can handle a wide range of products. They are ideal for transporting items of various sizes and shapes, especially when smooth and continuous motion is required.
2. Roller Conveyors (Powered): Unlike their gravity-operated counterparts, powered roller conveyors use motorized rollers to move products. They are excellent for heavy or bulky items and can be adjusted for speed and product spacing, making them suitable for assembly lines.
3. Slat Conveyors: Comprising slats attached to a chain, slat conveyors offer a flat and stable surface for products to rest on as they move. This type is particularly beneficial for heavy or oddly shaped items that require additional support.
4. Chain Conveyors: Ideal for heavy loads, chain conveyors use a series of chains to transport pallets or large items. They are robust and capable of handling high-capacity loads, making them a go-to for heavy manufacturing sectors.
Gravity Conveyors: Types and Applications

Gravity Conveyors utilize the force of gravity to move items and do not require any external power source. They are cost-effective, easy to install, and maintain, but offer less control over speed and product flow. Key types include:
1. Roller Conveyors (Gravity): These conveyors consist of rollers mounted on a slight incline, allowing items to move down due to gravity. They are best suited for lightweight items and are commonly used in warehousing and pick-and-pack operations.
2. Skatewheel Conveyors: Featuring small wheels in a series, skatewheel conveyors are flexible and lightweight. They are ideal for lighter loads and can easily adjust to different layouts and curves.
3. Chute Conveyors: Chute conveyors are inclined channels or troughs that leverage gravity for rapid item descent. While efficient for quick movement, they offer minimal control and are best for sturdy items that can withstand impact.
Choosing Between Motor Driven and Gravity Conveyors
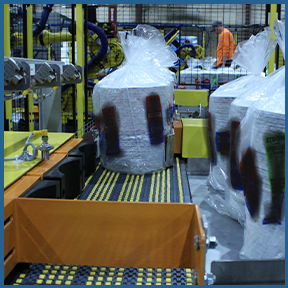
Example of integrating motor-driven mattop with skatewheels for low back pressure in areas of accumulation.
Factors to Consider:
- Product Characteristics: Size, weight, and shape of the items being transported.
- Speed and Efficiency: Required pace of the manufacturing process.
- Control and Accuracy: The degree of control needed over product movement.
- Cost: Budget constraints and overall cost-effectiveness.
Tips for Successful Integration and Maintenance:
- Ensure compatibility with existing automation systems and future scalability.
- Regularly inspect and maintain conveyor components for optimal performance.
- Train staff on safe operation procedures and emergency stop mechanisms.
Conclusion
Selecting the appropriate conveyor system is crucial for maximizing productivity and efficiency in robotic automation systems. Motor Driven Conveyors offer greater control and versatility for diverse manufacturing needs, while Gravity Conveyors provide a simple, cost-effective solution for straightforward transportation tasks. By carefully considering the specific requirements of your product manufacturing process, you can ensure the successful integration of a conveyor system that enhances operational flow and meets your production goals.
Request Quote ---- JOIN OUR MAILING LIST ---- Contact Us